Precision micro lathes are important technical equipment for the realization of high-precision micro-parts. In recent years, they have received more and more attention from all over the world. Developed countries such as the United States, Europe and Japan have developed and produced a variety of precision micro-machine tools since the 1990s. Spindle rotation in 1998 In order to successfully complete the coronary stents and industrialization of the major scientific and technological projects in Dalian, the group proposed the development of the sub-class precision micro lathe for this class; the spindle rotation accuracy is required to be 0.5, and the typical machining parts are required. A 52-piece part.
1The overall layout of the machine tool is optimized by the precision micro lathe, the bed rail system, the spindle system; the feed and micro-motion tool holder system; the numerical control system, the laser detection system, the vibration isolation system, and the optical tool setting system. section. Its overall layout optimization 1.
1 bed; 2, to the slide; 3, to the servo motor; 4, to the laser probe; 5, to the laser mirror; 6 vacuum suction cup; 7 headstock; 8 magnetic coupling, 14 9 spindle motor seat; 102-direction laser mirror; spindle motor; 122 to laser probe; 132 to feed servo motor; 14 micro-motion tool holder; 15 optical imaging tool setting system, male, person, university professor of mechanical engineering, Ph.D.
2 Spindle system According to the overall design performance requirements of the machine tool, the main technical indexes of the machine tool spindle should reach the radial and axial runout of the spindle less than 025 qing; the spindle speed is 3000 〃, stepless speed regulation.
In order to meet the above spindle precision requirements, the spindle components are optimized, 2 is the overall 1 vacuum suction cup of the spindle parts; 2 spindle box; 3 flexible coupling; 4 drive motor layout. According to the overall layout requirements of the machine tool, the spindle component is mounted on the longitudinal slide 2 to become a moving part. The spindle motor is separated from the spindle box, and the spindle box is connected to the motor through a flexible coupling. The purpose is to eliminate the influence of motor heating on the spindle accuracy.
The main shaft bearing adopts an aerostatic bearing. Its structure is a cylindrical surface radial thrust type. The front and rear radial bearings adopt a double bearing coaxial sleeve structure, which can ensure the coaxiality requirement well. The specific parameter determination process is to first design the parameters by engineering calculation method, and then use the finite element method to accurately calculate the bearing.
The flexible coupling is magnetically coupled, the magnetic coupling is a permanent magnet type, and has a series of advantages such as a non-heating structure compared with an electromagnet.
The 3 bed rail system is determined according to the overall technical requirements of the machine tool and the overall plan. The bed rail is selected from the layout of 3. The machine tool adopts a flat configuration, and the vertical and horizontal slides move independently. The vertical slide moves the spindle box along the 2 axes, and the horizontal slide moves the knife holder along the parent axis without mutual interference.
Both the bed and the guide rail are made of ball-milled cast iron, and the guide rail surface is plasticized; the static pressure air-floating guide rail is selected on the structure, and the structural parameters are optimized by the finite element method. The following two factors are considered: the throttle method and the section. The influence of the flow aperture on the performance of the guide rail; the influence of the pressure distribution at the position distribution of the orifice on the performance.
4 Feeding and micro-motion tool holder system feed system realizes the slip direction of the slide and the movement, the technical index requires the displacement resolution 0.0 guide straightness full error 0.2 spleen; for this design, 1 company's communication The servo motor is driven to drive a ball screw with a pitch of 2, which realizes the feed motion of the vertical and horizontal slides respectively.
The micro-feeding tool holder system selects the micro-displacement motion module of 1 company. The module adopts piezoelectric ceramic as the driving component, and pushes the tool holder to realize micro-displacement. The maximum displacement is 30, and the tool holder is equipped with a tool height fine adjustment mechanism. The continuous adjustable range is 2 stomachs; with the tool centering, an optical imaging system is designed to adjust the cutting point of the turning tool. The 5 CNC system design control system includes two parts: the overall logic control system and the motion control system. The overall logic control system is used to ensure and coordinate the normal working sequence between the subsystems. The motion control system mainly implements the motion trajectory generation and servo control functions. The logic control part is adopted as a controller, and communicates with the main control computer through the digital interface board, the microcomputer is used as the main control unit, and 4 is the main control system frame.
Input and output circuit input and output circuit network, input and output circuit machine tool operation panel, strong electric circuit, motor relay, etc. 1 = spindle speed control unit, spindle motor, servo drive unit, servo motor, 6 vibration isolation system, vibration isolation system, air spring As the vibration isolation component, the corresponding machine tool level adjustment device is designed, the dynamic model of the system is established, and the natural frequency of the air spring vibration isolation system is theoretically calculated to determine the optimal damping parameter.
7 Conclusions This design proposes the technical specifications of precision micro lathes according to the requirements of the parts to be machined; and uses the modular design cycle to make the design and production of the machine more flexible.
(Finish)
Manual Stage Chain Hoist is specially designed & manufactured for stage inversion or common lifting operation purpose. for example, in stage stereo, lighting, show banner,
campaign activity and steel frame which application is very wide.
1. Clutch: Protects hoist, operator, structure from damaging overloads.
2. With Overload Protection: Designed to prevent lifting of excessive overloads. Helps prevent lifting of dangerous loads.
3. Zinc plated Load Chain to protect against corrosion. Optional black finish available.
4. Low voltage control: 24 and 48 volt optional.
5. Cast aluminum housing, lightweight. Black power coated finish for low visibility.
6. 5-teeth Lifting Chain wheel
7. Double brake: With mechanical brake
Products ahow
Our Services
1.Client
We treasure and try to understand all the different needs of our clients and seek to forge a long term professional relationship with them. The satisfaction of each and every customer is our main goal and motivation in conducting our business.
2. People
We work as a team and treat each other with respect. Our solid, capable and knowledgeable team is valued as the greatest asset and an integral part of the business.
3. Product
Our products are of HIGH quality standards and always come with certificate of compliance by the manufacturers.
4. Performance
We aim to achieve high level of performance and satisfaction to both our client and people, which include delivering high quality services and treating people with integrity.
5. Free sample and OEM service
We can provide free samples to you and we also have OEM service, we can put your logo on the label and the information you need on the webbing too.
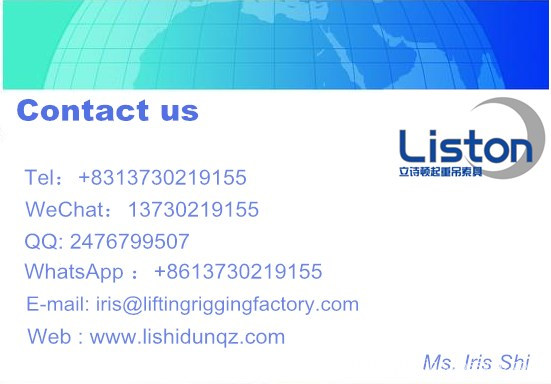
Stage Chain Hoist,Climbing Chain Hoist,Manual Stage Chain Hoist,Electric Stage Chain Hoist
Hebei Liston Lifting Rigging Manufacturing Co., Ltd. , https://www.liftingriggings.com