In 2004, Germany began to implement a subsidy program of 0.57 euros per kilowatt-hour for solar photovoltaic power generation, and the global photovoltaic industry quickly stepped into the gold channel. Soon, Japan and the United States have also issued plans to subsidize or encourage solar photovoltaic power generation.
In 2006, the actual output of photovoltaic cells in the world reached 2,600 megawatts, and the production capacity exceeded 3,000 megawatts; the output of photovoltaic cells in China was 450 megawatts that year, a net increase of 280% compared with 2005, and the production capacity of photovoltaic cells in China reached 1,200 megawatts; Production and capacity are 800 MW and 2000 MW.
According to the latest statistics from international authoritative PV magazine PHOTON International, Wuxi Suntech's component production capacity ranks first in the world, and its cell manufacturing has risen from No. 6 to No. 3 globally, surpassing multinational companies such as Kyocera, Sanyo, and BP SOLAR. The company's annual production capacity of photovoltaic cells increased from 150 MW at the end of 2005 to 270 MW at the end of 2006, an increase of 80%. It is not difficult to find that the company’s output is only half of the production capacity. Similarly, half of the equipment in most companies is idling. This is due to the tight supply of upstream silicon wafers.
Despite the huge output, the overall profits of Chinese solar manufacturers are low. Because the popularity of upstream raw materials has increased a lot of procurement costs.
One of the manufacturing steps of crystalline silicon includes the refining technology of high-purity silicon. China's mastery of this technology is limited, so more than 90% of crystalline silicon raw materials must be imported and most of solar companies have only 5% to 6% of profits. .
However, upstream manufacturers with purification technology have made their mark. Wacker Chemicals, the world's third-largest high-purity silicon processing company, increased its polysilicon sales by 13% in 2006 to 326 million euros, and its profit increased to 118 million euros, a 31% increase. The company also plans to expand its production capacity from an annual output of 5,500 tons to 6,500 tons.
The photovoltaic effect released by Suntech in Wuxi made people see a huge magnetic field in the capital market. Chinese PV manufacturers have become the new main force following China’s IT companies. They have again set off a climax in overseas listings: Jiangsu Aters, Jiangsu Linyang, Changzhou Tianhe, and Jingao New Energy, etc. Yingli, Nanjing Zhongdian, etc. will continue to impact the US stock market.
After China has become the world's three largest processing bases for photovoltaic cells, it is possible to achieve long-term growth of the entire industry only by expanding and stabilizing the supply of raw materials. From 2004 to 2006, the price of polysilicon increased by 5 times. At the same time, due to the high cost of upstream crystalline silicon, the prices of downstream products must be brought in line with ordinary electricity prices, and this industry cannot be quickly promoted in China.
Zhao Ying, director of the Institute of Optoelectronic Thin Film Devices and Technology at Nankai University, told reporters that the development of high-efficiency, low-cost thin-film solar cells is the development direction of photovoltaic power generation. Of the existing thin-film solar cells, the only thin-film solar cell that realizes large-scale production is silicon. Thin film battery. In 2004, the output of amorphous silicon thin-film batteries exceeded 45 megawatts, but last year the industry witnessed a catastrophic development. Japan’s Kaneka plans to expand amorphous silicon and amorphous silicon/microcrystalline silicon stacking capacity to 70 megawatts in 2008.
Injection Tooling & Mold Design
Professional injection molding customized products for 20 years, to provide you with a reassuring customized experience, in order to ensure product quality, the company strictly follows the ISO9001:2015 quality management system for management, one-stop service for assembly and packaging, free design for large quantities, affordable prices, and high quality Guarantee is your trusted source manufacturer.
Fast quotation, medical, electronic, automotive, household mold injection molding customization. Professional injection molding customized products for 20 years, to provide you with a reassuring customized experience. With many years of industry production experience, we can process and order according to drawings and samples, source manufacturers, quality assurance, complete specifications, high-quality after-sales service, modern complete sets of production equipment and superb workforce, with an annual production capacity of nearly 1,000 tons. Liquid silicone vulcanization molding equipment, injection molding process, extrusion/extrusion.
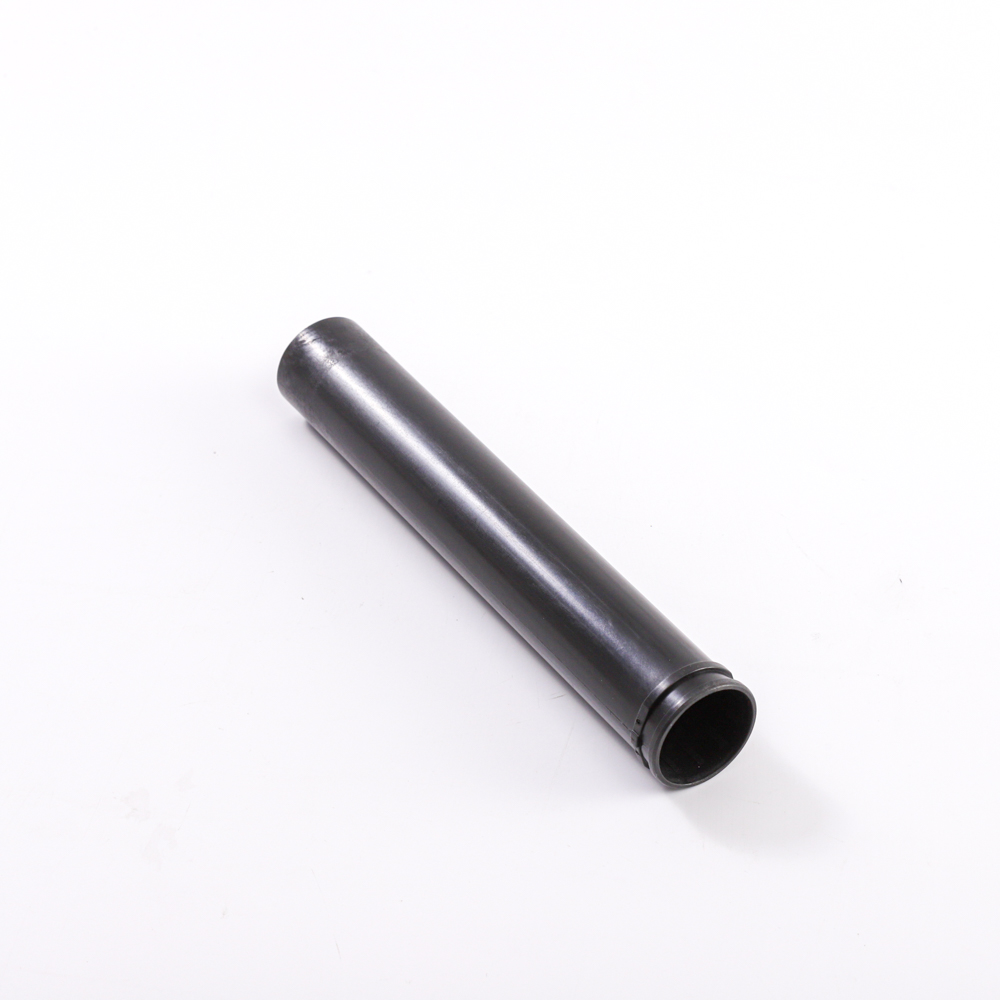
Injection Tooling & Mold Design,Injection Molding Tooling Design,3 Plate Injection Mold Design,Injection Molding Die Design
Suzhou Dongye Precision Molding Co.,Ltd. , https://www.sjdongye.com