High aluminum tiles are the best material to replace silica bricks
A neutral refractory material with an alumina content of more than 48%. By bauxite or other high alumina content of raw materials formed and calcined. High thermal stability, refractoriness above 1770°C. Good slag resistance. Used for masonry lining of steelmaking furnaces, glass furnaces, cement rotary furnaces, etc.
Mainly used for masonry blast furnace, hot air furnace, electric furnace top, blast furnace, reverberatory furnace, rotary kiln lining. In addition, high-alumina bricks are widely used as refrigerated lattice bricks for open hearth furnaces, plug heads for gating systems, and nozzle bricks. However, the price of high-aluminum tiles is higher than that of clay bricks, so high-aluminum tiles need not be used where clay bricks can meet the requirements.
Silica bricks have a silicon dioxide content of over 93%. The true density is 2.38g/cm3. With anti-acid slag erosion performance. High temperature strength. Load softening starting temperature 1620 ~ 1670 °C. Long-term use without deformation at high temperatures. More than 600 °C generally no crystal transformation. Smaller temperature expansion coefficient. High thermal shock resistance. Crystal transformation below 600°C is more, volume change is larger, and thermal shock resistance is worse. The natural silica is used as raw material and an appropriate amount of mineralizing agent is added to promote the conversion of quartz in the green body to phosphorus quartz. It was slowly fired at 1350 to 1430°C under a reducing atmosphere.
Mainly used for coke oven and combustion chamber partitions, steel regenerator regenerators and slag chambers, soaking furnaces, glass melting furnaces, refractories, ceramic kiln furnaces, etc. Bearing location. It is also used for hot blast furnace high-temperature load-bearing parts and acid open hearth roofs.
As for whether high aluminum tiles can replace silicon bricks, the key is to use some of the process parameters. Because of the stringent requirements for temperature rise of silicon bricks, the temperature rise is slow, especially when the temperature is within 300 degrees, and the resistance to quenching and rapid thermal performance is poor. The advantages are high temperature resistance and alkali resistance. High-alumina bricks will shrink at high temperatures and heat preservation, and attention should be paid to large-span parts. In an alkaline atmosphere, it is easy to peel off, especially bricks containing aluminum.
High aluminum content, high operating temperature.
If the maximum operating temperature is up to 1400°C, it is not a long-term use and occasional ceasefire or cooling is required. The use of high-aluminum ceramic tiles instead of silica bricks is certainly better than silica bricks.
Company Name: Gongyi Hongfa Minerals Co., Ltd Tel: +86-0371-85610369
Fax: +86-0371-85610369
Cell phone
High aluminum tile mailbox: [email protected]
Business QQ:5595115
Address: Hetaoyuan Development Zone, Gongyi City, Henan, China
We have many years manufacturing experiences on aluminum alloy heatsink parts
our mature technology on aluminum profile extrusion make our Heatsinks components brand very popular at our domestic market. And we also export to EU, US and other Asian markets. With strong engineering team on extrusion heat sink, we have been provided our customers very excellent services many years.
Our heat sinks are with various shapes, and we are also good at large heatsinks as well. Our large heatsinks are of stable quality and applied for different industries, we look forward to supporting you on heat sink parts.
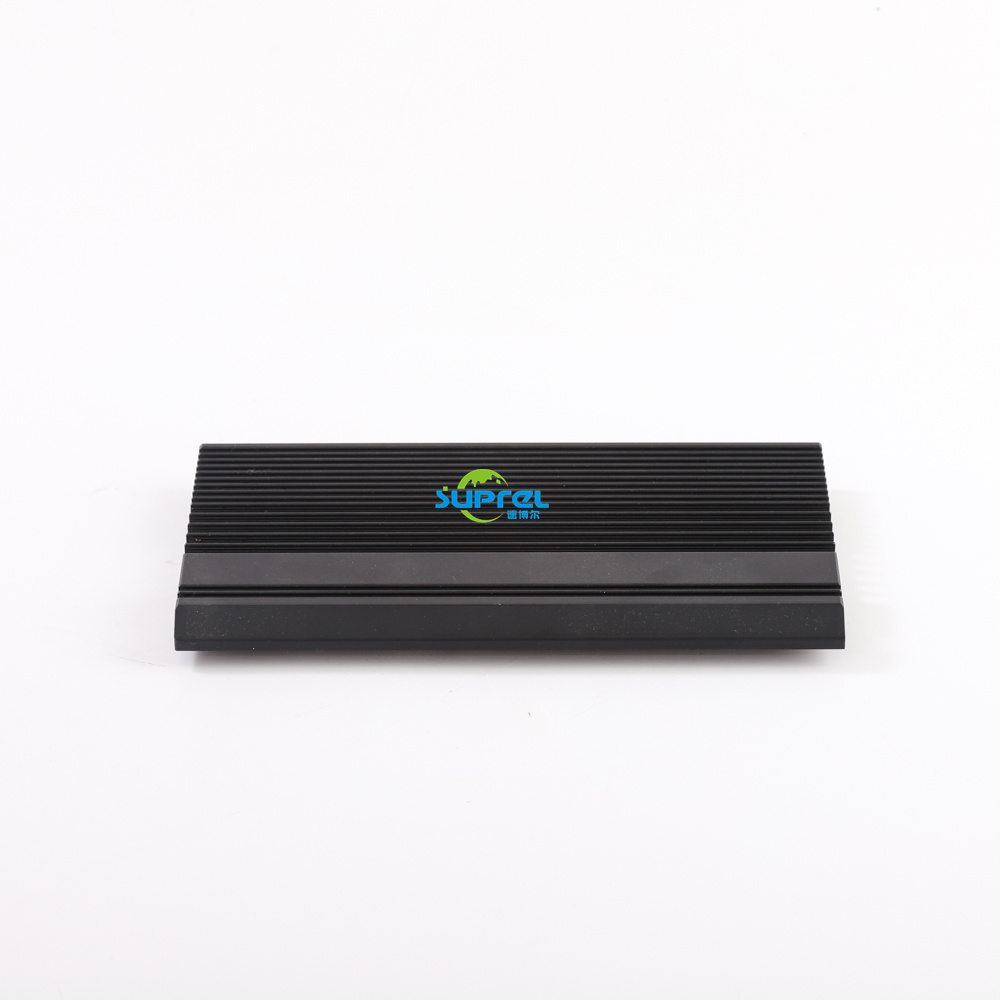
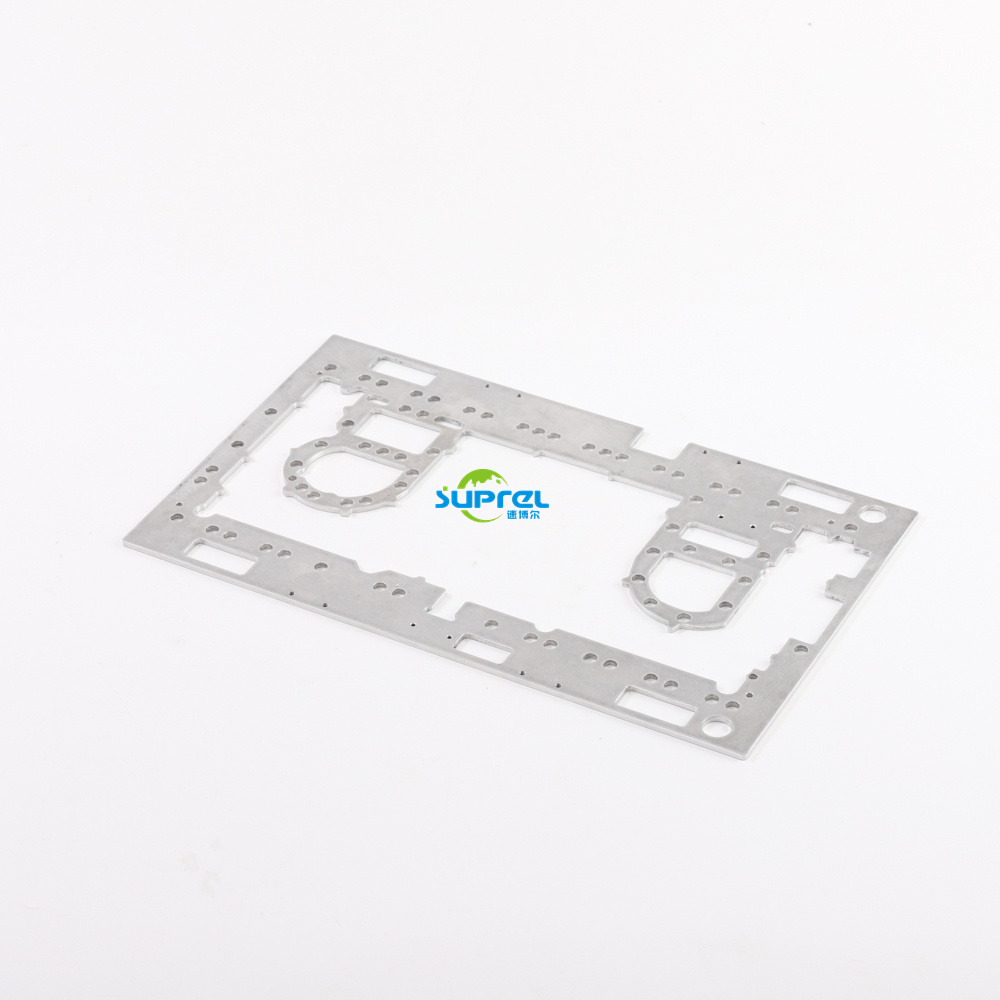
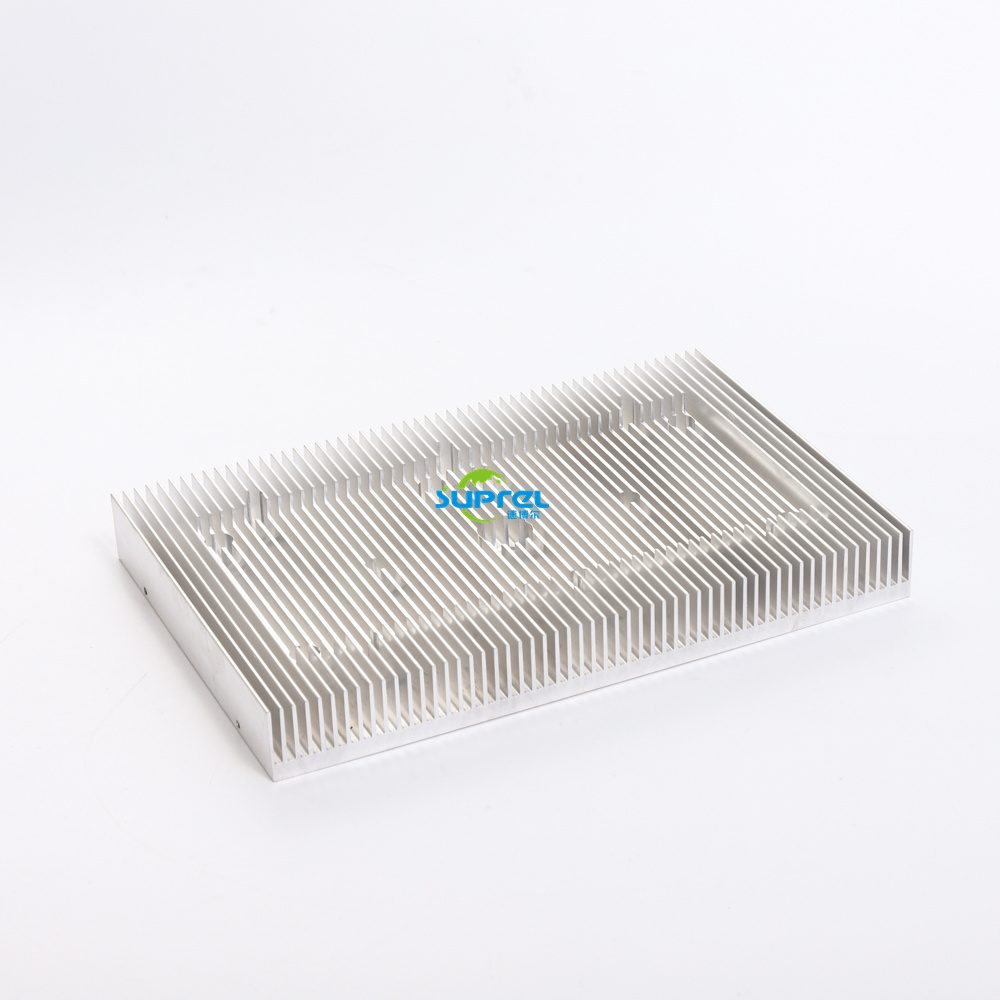
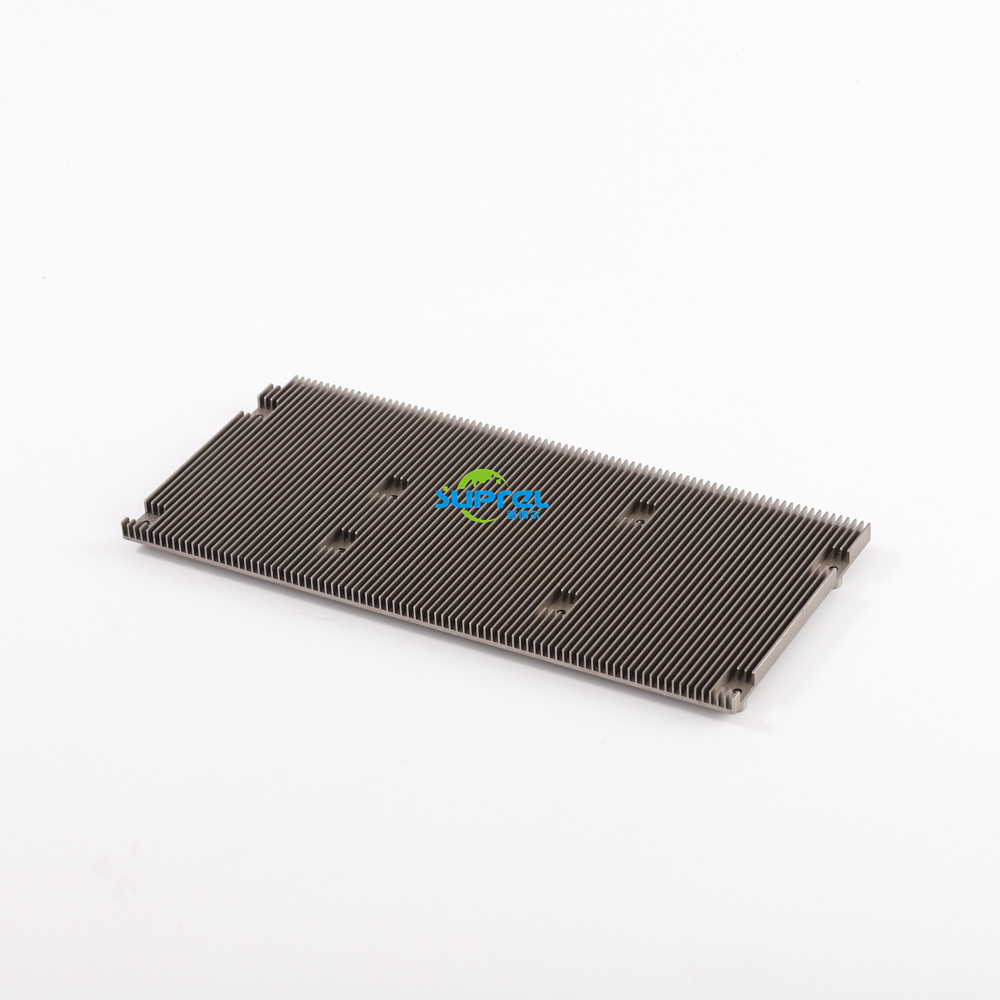
Large Heatsinks,Large Aluminum Heat Sink,Large Aluminium Heat Sink,Big Size Heat Sink
Suprel Metalwork Co., Ltd , https://www.suprel-cool.com