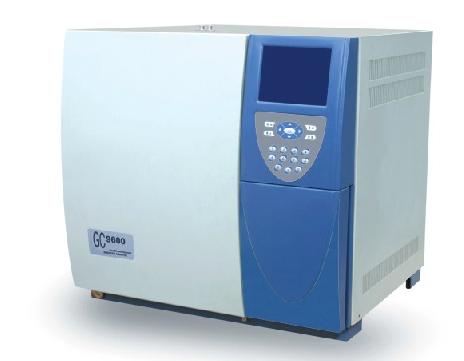
First, the instrument's internal purge and cleaning
After the gas chromatograph is shut down, open the side and rear panels of the instrument and use the meter's air or nitrogen to purge the instrument's internal dust. Use a soft bristled brush for areas where there is more dust or where it is not easily purged. After the purging is completed, scrubbing with water or organic solvents in the area where the organic substances are contaminated in the instrument can be performed by wiping the water-soluble organic materials with water. If the organic solvent can not be thoroughly cleaned, the organic solvent can be used for treatment. It is not water-soluble or possible. Organic chemicals that react with water are cleaned with organic solvents that do not react with them, such as toluene, acetone, and carbon tetrachloride. Note that the surface or other components of the instrument must not be eroded or recontaminated during wiping.
Second, the circuit board maintenance and cleaning
Before the gas chromatograph is ready for inspection, shut off the power of the instrument and first use instrument air or nitrogen to purge the circuit board and circuit board slots. Use a soft bristled brush for the dusty parts of the circuit board and slot. Carefully clean up. Wear gloves as much as possible during operation to prevent static electricity or perspiration on hand from affecting the components on the circuit board.
After the purge is completed, the use of the circuit board should be carefully observed to see if the printed circuit board or electronic components are significantly eroded. The electronic components contaminated with organic substances on the circuit board and the printed circuit are carefully wiped with alcohol-absorbent cotton, and the circuit board interface and slot department are also wiped.
Third, the injection port cleaning
During the inspection, it is necessary to clean the glass liner of the gas chromatograph inlet, the manifold plate, the inlet line of the inlet, EPC and other parts.
Glass Liner and Diverter Plate Cleaning: Carefully remove the glass liner from the instrument and carefully remove glass wool and other contaminants from the liner with tweezers or other small tools. Do not scratch the liner surface during removal.
If the premise permits, the glass liner that has been cleaned up can be cleaned with ultrasonic waves on top of organic solvents and used after drying. It can also be cleaned directly with organic solvents such as acetone and toluene, and dried after cleaning.
The best cleaning method for the shunt plate is to use ultrasonic treatment in the solvent and use after drying. You can also choose a suitable organic solvent cleaning: After the splitter plate is pulled out from the inlet, it is first cleaned with an inert solvent such as toluene, then cleaned with an alcohol solvent such as methanol, and used after drying.
Diversion line cleaning: When gas chromatography is used to analyze organics and macromolecules, many organics have a low freezing point. During the process of venting a sample from a gasification chamber via a diverter line, the organics of the department solidify in the diversion line.
After a gas chromatograph has been used for a long period of time, the inner diameter of the diverting line gradually becomes smaller or even completely blocked. After the flow of the bypass line is blocked, the instrument inlet shows an abnormal pressure and the peak shape is degraded. The analysis result is abnormal. During the inspection process, the shunt line needs to be cleaned regardless of whether it can determine whether the shunt line is clogged.
Diversion line cleaning generally chooses organic solvents such as acetone and toluene. It is difficult to clean the shunted pipelines that are sometimes clogged with simple cleaning methods, and some other auxiliary mechanical methods are required to complete them. It is possible to select a wire of suitable thickness for the simple dredging of the split line and then to clean it with an organic solvent such as acetone or toluene. Because it is not easy to make correct decisions on the conditions of the shunting department in advance, it is necessary for the manual diverter gas chromatograph to clean the diverter line during the inspection process.
For gas chromatographs with EPC-controlled shunts, prolonged use may allow some small injections of rags to enter the EPC interface with the gas line, possibly blocking the EPC department or causing pressure changes in the inlet.
Mobile Asphalt Mixing Plant is a convenient, efficient and mobile asphalt mixture production equipment, which is suitable for all kinds of road construction and maintenance projects. It has the characteristics of strong mobility, quick installation and easy operation, and can provide high quality asphalt mixture for the project and improve the construction efficiency.
Mobile Asphalt Mixing Plant is mainly composed of mixing host, dosing system, fuel system, support device and dust removal system. Among them, the mixing machine is the core part, which is responsible for mixing various raw materials evenly to produce high-quality asphalt mixture. The dosing system is responsible for adding various raw materials to the mixing machine in a certain proportion. The fuel system powers the entire device, usually using diesel or gasoline. The support unit includes four wheels and a suspension system that allows the device to travel and operate in a variety of terrain conditions. The dust removal system is responsible for collecting dust and exhaust gas generated during the production process to ensure a clean working environment and air quality.
The working process of the mobile asphalt mixing station mainly includes the following steps: First, the various raw materials are prepared and added to the mixing machine through the dosing system. Next, the mixer machine starts to work, mixing the raw materials evenly to produce the asphalt mixture. The asphalt mixture is then transported to the construction site for road paving or maintenance. In the whole process, the operation of the mobile asphalt mixing plant is simple and convenient, and it can be quickly deployed and moved, which greatly improves the construction efficiency.
Compared with the traditional fixed asphalt mixing plant, the mobile asphalt mixing plant has the following advantages: First, it has the characteristics of strong mobility and rapid deployment, and can adapt to a variety of complex terrain and construction environment. Secondly, the installation and disassembly of the mobile asphalt mixing plant is very convenient, and the transfer and installation of the equipment can be quickly completed, reducing the construction time. In addition, the operation of the mobile asphalt mixing plant is simple and easy to maintain, reducing the skill requirements of the operator and maintenance costs.
In short, the mobile asphalt mixing plant is an efficient, convenient and mobile asphalt mixture production equipment, which is suitable for all kinds of road construction and maintenance projects. It has many advantages, can provide high quality asphalt mixture for engineering, improve construction efficiency, and has a wide range of application prospects.
Recycled Asphalt Mixing Plant,Asphalt Mixing Facilities,Stationary Asphalt Mixing Plant,Asphalt Mixing Facilities Stationary
BituRock Science & Technology (Jiangsu) CO., LTD , https://www.biturockequipment.com