Design
Yubei Power Plant adopts the factory-wide auxiliary workshop networking control method to conduct centralized real-time monitoring of the auxiliary workshops in the centralized control room of the power plant. The chemical water treatment station is a large subsystem of the auxiliary workshop control system. This article mainly introduces the program and design of the chemical water treatment program control.
I. Process System Overview
The chemical water treatment process system consists of the following systems:
1. Boiler make-up water treatment system
Includes reverse osmosis pre-desalination system and chemical desalination system.
2. Weak acid and sidestream pretreatment system
The side stream treatment system is divided into two parts, one part is the clarification filtration pretreatment system, and the other part is the weak acid resin treatment system.
3, chemical waste water centralized treatment system
It is divided into regular acid-alkali wastewater treatment, weak acid treatment system regeneration wastewater treatment, and non-recurrent drainage treatment.
4, recycled water plus sodium hypochlorite system
Second, the program of chemical water treatment program control
Chemical water treatment station control system uses computer program control (programmable controller PLC + PC monitoring station). In the centralized control room of the power plant, centralized monitoring of chemical water treatment and various systems such as coal, ash, and oil is performed through operator stations on the plant-wide auxiliary plant monitoring network, and conventional control dashboards are no longer provided. In order to achieve automatic control of subsystems in the upper auxiliary shop network failure, the chemical water treatment station has a lower-level monitoring network, connects each sub-control system, and is equipped with two local upper-level computers. Normally, control of the chemical water treatment process systems is implemented on the upper network operator station (central control room). When it is abnormal, it operates on the lower network operator station.
The control equipment room is located between Columns 2 to 5 in Columns C and D in the Chemical Water Treatment Area Laboratory Building, with an area of ​​about 60m2 and an elevation of 0m. Next to the control room, an area of ​​27m2, set up two consoles on the console.
Third, chemical water treatment program control system composition
Chemical water treatment terminus program control system is provided by Beijing Huaneng Xinrui Control Technology Co., Ltd.
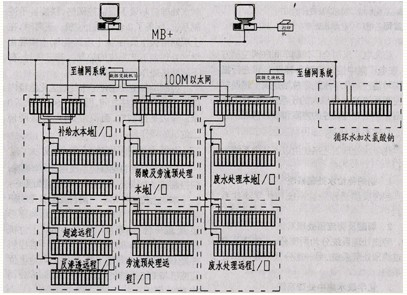
The local upper monitoring station uses two mutually-standby Advantech IPCs. The CRT is DELL's 21-inch industrial-grade flat color display and is equipped with an A4 color inkjet printer. The upper computer runs in the Chinese version of Windows 2000. The monitoring software is Intellution's IFIX software uses the Modicon's MB+ network for the local host monitoring and PLC systems.
PLC uses MODICON Quantum series, the controller CPU model is 140CPU43412A (Intel 486, 66MHZ frequency, 2M memory), the control network's underlying network is a single MB+ network, the upper network is 100M industrial Ethernet, the subsystem's Ethernet communication interface The redundant configuration of the card can automatically switch to another line when a network line fails to communicate, which does not affect the monitoring of the system by the upper layer network.
The PLC is divided into four sub-control systems according to the process system. Each sub-system is equipped with a master control station and a remote I/O station. The remote I/O network adopts a dual-cable configuration. The main control station is arranged in the chemical water treatment zone control equipment room.
Each control subsystem of the chemical water treatment station is configured as follows:
1, make-up water treatment subsystem
The makeup water treatment subsystem includes the main station of the makeup water treatment system, and the remote I/O station of the ultrafiltration and reverse osmosis systems.
The CPU of the makeup water treatment master station is hot standby and the number of cabinets is two. Local I/O module monitoring includes fresh water tanks, fresh water pumps, positive beds, negative beds, mixed beds, demineralized water pumps, and reverse osmosis flush water pumps.
One remote I/O station is set in each of the ultrafiltration zone and the reverse osmosis zone. The ultrafiltration zone has two cabinets and one reverse osmosis cabinet. The remote I/O station monitors clean water tanks, freshwater tanks, freshwater pumps, backwash pumps, weak acid pumps, sodium hypochlorite system pumps, ultrafiltration units, and reverse osmosis units.
2. The side-stream and pretreatment subsystems of circulating water include the main station of the circulating water treatment system, and the remote I/O station for circulating water by-pass pretreatment.
The main station of the circulating water treatment system uses a single CPU and the number of cabinets is 2. The local I/O module monitors weak acid positive beds, decarbonizers, stabilizer dosing devices, concentrated sulfuric acid metering boxes, metering pumps, and transfer pumps.
A remote I/O station is installed in the booster pump room of the sidestream pretreatment zone. The number of cabinets is 1. The coagulant and coagulant dosing system, gravity filter tank, backwash recovery tank, clear water tank, and clear water pump are monitored. Backwash pumps, Roots blowers, submersible pumps, etc.
3, wastewater treatment subsystem
The wastewater treatment subsystem includes the main station of the wastewater treatment system and the remote I/O station of the wastewater storage tank.
The main station of the wastewater treatment system adopts a single CPU, local I/O module to monitor the neutralization tank, clean water tank, wastewater treatment Roots blower, coagulant, coagulant aid, and sodium hypochlorite dosing device. High acid storage tanks, high storage tanks, hydrochloric acid metering boxes and injectors, lye tanks and injectors, dewatering machines.
A remote I/O station is set in the sludge pumping station of the waste water storage tank, the number of cabinets is 2, and the waste water storage tank, mechanical acceleration clarifier, clarifier sludge pump, concentration tank, and sludge pump are monitored.
4, circulating water plus sodium hypochlorite control system
The circulating water plus sodium hypochlorite control system adopts a single CPU. The PLC is equipped with process equipment. The selection is the same as other subsystems. It can be directly connected to the monitoring network and the cabinet is installed in the sodium hypochlorite workshop.
The I/O point statistics of each control system are shown in the following table:
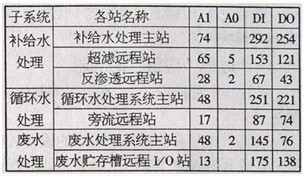
The circulating water plus sodium hypochlorite station is supplied with the equipment, and the I/O point is unknown.
Fourth, chemical water treatment program control function
The control system performs centralized monitoring, management, and automatic program control of the entire chemical water treatment process system. Specific functions include:
1, control and operation functions
1.1 Control of sequential operation equipment
For gravity-type filters, reverse osmosis devices, ion exchangers and other devices that require sequential operation, the control operations include automatic, single-step, remote manual, or manual on-site methods.
The automatic mode is the control mode that the system automatically completes a series of operations according to the operator's instructions. After the automatic cleaning or regeneration process of the equipment is started, a series of operations will be automatically performed according to the requirements of the step sequence table, including the acid and alkali in the acid and alkaline measuring tanks. After the cleaning or regeneration is completed, it automatically goes into standby state. When programmed, the failed device can automatically stop running. In the single-step mode, the system completes a certain step in the step list according to the operator's instructions, including the switch of the valve and the start-stop of the motor. Remote manual refers to the start and stop of the motor and the opening and closing of the valve with a mouse on the screen.
1.2 Control of pumps, fans and valves
For all electric/pneumatic valves, fans, pumps and other equipment in the process system, program (remote) control and local control can be performed. For pneumatic valves, control can also be performed on the solenoid valve box, providing necessary protection in the control logic. And locking means.
The control of the water pump and the fan are automatically interlocked to start, remote manual, manual in several ways. When the pump or fan installed in the mother pipe is in the automatic interlocking start mode, if a motor stops due to a fault during operation, the motor in the interlock standby state is automatically started.
1.3 Power Control
The control, measurement and protection of the factory power supply 380V incoming line and the contact circuit breaker in the area of ​​the chemical water treatment station are hardwired into the boiler make-up water treatment control system, and the switching of the power supply system in the area is realized in the boiler make-up water treatment control system. , monitoring.
2, display function
All status information of the control system is displayed on a 21-inch display. The screen includes process flow diagram screens, operation screens, alarm display screens, and process parameter curves. It can display the process flow of each subsystem separately and collect the operating conditions of the system at any time, and realizes equipment accident alarms, process analysis, and systems. Fault detection, alarm management, report generation, operating condition recording, system parameter setting, and operation of equipment.
2.1 Process Flow Chart Screen
The process flow picture includes the general picture of the subsystem, the diagram of each subsystem, etc.
The flow chart shows the status of the valves and motors through different colors. The measurement values ​​and engineering units of the relevant meters, as well as the cumulative values ​​of the relevant flows, are also displayed on the screen.
2.2 Operation screen
The screen for system operation includes a device operation screen and an equipment overhaul window.
The system operation screen includes operation buttons such as a device selection button, a single-step operation button, an automatic operation button, and a delay button. When the cleaning or regenerating step is performed, the time for this step will be displayed on the screen.
2.3 Service Status Setting Screen
For large devices such as ion exchangers, they can be set on the screen for maintenance. Equipment that is in the maintenance state, the operator can't perform any operation on it at the moment, and can be operated only when the maintenance state is cancelled. The maintenance screen includes all device buttons that can be set to service status. Click the button of a device to set it to the maintenance status. Equipment that is under overhaul status changes its color when it is overhauled.
2.4 Step time modification screen
The step time modification screen has all the relevant steps and the setting values ​​of various types of sequential operation devices.
3, failure judgment and interlock function
The control system can judge whether it is ineffective according to the effluent quality of the relevant equipment such as ion exchangers (needs the on-line monitor table), differential pressure at the inlet and outlet, accumulated flow, or cumulative operating time. The failed device will alarm and can automatically stop running.
4. Manual intervention in sequential control
When the sequential control step is performed automatically, manual intervention such as stepping and stepping may be performed as needed, and the time and sequence of the originally set steps may be temporarily changed.
5, the time can be modified online.
V. Selection of instruments and local control equipment
There are two sources of chemical water meters and on-site control equipment at Qinbei Power Plant. Some of them are supplied with process equipment, and some are provided by program-controlled equipment manufacturers.
1, solenoid valve box
The electromagnetic valve box is equipped with an air source isolation valve, a gas source triple piece, and a cartridge type dual-control solenoid valve (including a bus plate). Valve position indicators (two-color light: red for on, green for off), valve operation knobs, local/remote switching knobs, etc. are mounted on the front panel.
Reciprocating pneumatic cylinder valves, such as pneumatic butterfly valves and ball valves on site, are controlled by dual-control, two-position, five-way solenoid valves. Pneumatic diaphragm valves could have been controlled by two-position three-way solenoid valves. In order to reduce the number of solenoid valves for the control system in the unified system, all solenoid valves were controlled by dual-control five-way solenoid valves.
2, chemical analysis instruments: All adopt flow-type instrument. Both the silicon meter and sodium meter, on-line COD meter, and turbidity meter use imported products. Conductivity meters, pH meters, and acid-base concentration meters use domestic products. Analytical instruments are equipped with instrument cabinets, front glass door type, you can view the data at any time but also to facilitate the protection of the instrument.
3, other instruments
The transmitter is Rosemount 3051; the level gauge uses a two-wire ultrasonic continuous level gauge or remote magnetic level gauge; the flow measurement device uses the imported power-bar flow measuring device (outdoor installed measuring device is equipped with a straight connection Three valve group); The remote temperature measuring element adopts a two-wire integrated temperature transmitter to improve the signal anti-interference ability and reduce the PLC module type.
Sixth, the design process should learn from the problem
In the chemical water program control design, the following issues are worth paying attention:
1. All the equipments and instruments in the Chengbei Power Plant Programmable Control are provided in complete sets. However, due to the large number of process systems, there are many control devices and instruments brought by the equipment manufacturers. Therefore, despite the uniform requirements in the selection, Inevitably there is a difference in the actual order, which causes troubles for the subsequent maintenance and spare parts purchase.
2. In the ultrafiltration area, the supplier of the ultrafiltration equipment comes with a set of PLCs. Some I/O points are advanced with their own PLC, and then transferred to the ultrafiltration remote I/O station. Before the program control bidding, there was no information on the ultrafiltration equipment with its own PLC, so it was impossible to foresee it. It was suggested that when the process system was tendered, it was required that any PLC with its own PLC should indicate the detailed I/O content of the PLC at the time of bidding and provide A unified network interface; In addition, the process and program control bidding time should be as far apart as possible to improve the accuracy of the data.
3. The rationality of I/O point allocation. The water area is divided into several subsystems, and the subsystems are divided into local and remote stations. Therefore, the distribution of I/O points should be considered more carefully. It is necessary to take into account the integrity of the system and to consider the distance. Save on cables. In this design, I feel that some I/O points are not very convenient. For example, the power circuit of the pump is in the MCC cabinet, some in the PC segment, and the PC in the laboratory floor. However, the program-controlled manufacturers do not understand the electrical system. The interface is to allocate I/O points according to the location of the pump room.
4. Anti-jamming of remote I/O network in field applications
In the IDAS remote I/O network, the communication module, the front-end unit, and the communication line are all electrically isolated. There is no common ground problem between the front-end units, and mutual interference between the front-end units is completely avoided. The problem of ground return flow makes the entire network in a “full-floating†state and ensures reliable network communications.
The communication between the communication module and the FEP uses a special modulation and demodulation circuit and a balanced differential transmission method. The transmission level is high, peak-to-peak up to ±12V (RS485 transmission level is ±5V), plus perfect The verification method and automatic retransmission technology greatly improve the anti-interference ability of network communications. The most important point is that this special communication method ensures that the front-end and front-end machines do not communicate with each other, further ensuring the reliability of data transmission.
5. Fault self-diagnosis and online setting of remote I/O system
Through the extended serial port on the communication module, the user can modify or set the parameters of the front-end computer online without interruption of the data transmission of the DCS system. At the same time, the user can also observe the self-diagnosis information of the network online, which brings about extreme operation and maintenance of the system. Great convenience.
IV. Concluding remarks
To sum up, the communication module can ensure the real-time data transmission in the connection of remote I/O and DCS systems, increase the transmission level to enhance the anti-interference ability of the communication, and reduce the DCS system to the remote I/O. Functional burden. After a period of electricity, the actual use of the situation, convenient transfer, reliable communication, small size, easy installation and positioning, for the remote I / O and DCS system, reliable, fast connection has played an integral role.
Yubei Power Plant adopts the factory-wide auxiliary workshop networking control method to conduct centralized real-time monitoring of the auxiliary workshops in the centralized control room of the power plant. The chemical water treatment station is a large subsystem of the auxiliary workshop control system. This article mainly introduces the program and design of the chemical water treatment program control.
I. Process System Overview
The chemical water treatment process system consists of the following systems:
1. Boiler make-up water treatment system
Includes reverse osmosis pre-desalination system and chemical desalination system.
2. Weak acid and sidestream pretreatment system
The side stream treatment system is divided into two parts, one part is the clarification filtration pretreatment system, and the other part is the weak acid resin treatment system.
3, chemical waste water centralized treatment system
It is divided into regular acid-alkali wastewater treatment, weak acid treatment system regeneration wastewater treatment, and non-recurrent drainage treatment.
4, recycled water plus sodium hypochlorite system
Second, the program of chemical water treatment program control
Chemical water treatment station control system uses computer program control (programmable controller PLC + PC monitoring station). In the centralized control room of the power plant, centralized monitoring of chemical water treatment and various systems such as coal, ash, and oil is performed through operator stations on the plant-wide auxiliary plant monitoring network, and conventional control dashboards are no longer provided. In order to achieve automatic control of subsystems in the upper auxiliary shop network failure, the chemical water treatment station has a lower-level monitoring network, connects each sub-control system, and is equipped with two local upper-level computers. Normally, control of the chemical water treatment process systems is implemented on the upper network operator station (central control room). When it is abnormal, it operates on the lower network operator station.
The control equipment room is located between Columns 2 to 5 in Columns C and D in the Chemical Water Treatment Area Laboratory Building, with an area of ​​about 60m2 and an elevation of 0m. Next to the control room, an area of ​​27m2, set up two consoles on the console.
Third, chemical water treatment program control system composition
Chemical water treatment terminus program control system is provided by Beijing Huaneng Xinrui Control Technology Co., Ltd.
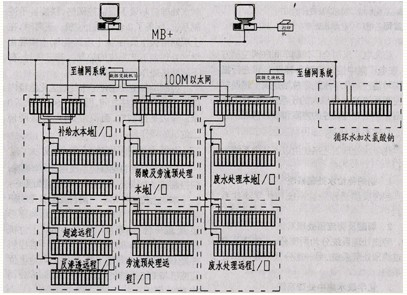
The local upper monitoring station uses two mutually-standby Advantech IPCs. The CRT is DELL's 21-inch industrial-grade flat color display and is equipped with an A4 color inkjet printer. The upper computer runs in the Chinese version of Windows 2000. The monitoring software is Intellution's IFIX software uses the Modicon's MB+ network for the local host monitoring and PLC systems.
PLC uses MODICON Quantum series, the controller CPU model is 140CPU43412A (Intel 486, 66MHZ frequency, 2M memory), the control network's underlying network is a single MB+ network, the upper network is 100M industrial Ethernet, the subsystem's Ethernet communication interface The redundant configuration of the card can automatically switch to another line when a network line fails to communicate, which does not affect the monitoring of the system by the upper layer network.
The PLC is divided into four sub-control systems according to the process system. Each sub-system is equipped with a master control station and a remote I/O station. The remote I/O network adopts a dual-cable configuration. The main control station is arranged in the chemical water treatment zone control equipment room.
Each control subsystem of the chemical water treatment station is configured as follows:
1, make-up water treatment subsystem
The makeup water treatment subsystem includes the main station of the makeup water treatment system, and the remote I/O station of the ultrafiltration and reverse osmosis systems.
The CPU of the makeup water treatment master station is hot standby and the number of cabinets is two. Local I/O module monitoring includes fresh water tanks, fresh water pumps, positive beds, negative beds, mixed beds, demineralized water pumps, and reverse osmosis flush water pumps.
One remote I/O station is set in each of the ultrafiltration zone and the reverse osmosis zone. The ultrafiltration zone has two cabinets and one reverse osmosis cabinet. The remote I/O station monitors clean water tanks, freshwater tanks, freshwater pumps, backwash pumps, weak acid pumps, sodium hypochlorite system pumps, ultrafiltration units, and reverse osmosis units.
2. The side-stream and pretreatment subsystems of circulating water include the main station of the circulating water treatment system, and the remote I/O station for circulating water by-pass pretreatment.
The main station of the circulating water treatment system uses a single CPU and the number of cabinets is 2. The local I/O module monitors weak acid positive beds, decarbonizers, stabilizer dosing devices, concentrated sulfuric acid metering boxes, metering pumps, and transfer pumps.
A remote I/O station is installed in the booster pump room of the sidestream pretreatment zone. The number of cabinets is 1. The coagulant and coagulant dosing system, gravity filter tank, backwash recovery tank, clear water tank, and clear water pump are monitored. Backwash pumps, Roots blowers, submersible pumps, etc.
3, wastewater treatment subsystem
The wastewater treatment subsystem includes the main station of the wastewater treatment system and the remote I/O station of the wastewater storage tank.
The main station of the wastewater treatment system adopts a single CPU, local I/O module to monitor the neutralization tank, clean water tank, wastewater treatment Roots blower, coagulant, coagulant aid, and sodium hypochlorite dosing device. High acid storage tanks, high storage tanks, hydrochloric acid metering boxes and injectors, lye tanks and injectors, dewatering machines.
A remote I/O station is set in the sludge pumping station of the waste water storage tank, the number of cabinets is 2, and the waste water storage tank, mechanical acceleration clarifier, clarifier sludge pump, concentration tank, and sludge pump are monitored.
4, circulating water plus sodium hypochlorite control system
The circulating water plus sodium hypochlorite control system adopts a single CPU. The PLC is equipped with process equipment. The selection is the same as other subsystems. It can be directly connected to the monitoring network and the cabinet is installed in the sodium hypochlorite workshop.
The I/O point statistics of each control system are shown in the following table:
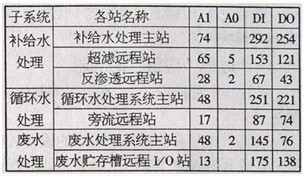
The circulating water plus sodium hypochlorite station is supplied with the equipment, and the I/O point is unknown.
Fourth, chemical water treatment program control function
The control system performs centralized monitoring, management, and automatic program control of the entire chemical water treatment process system. Specific functions include:
1, control and operation functions
1.1 Control of sequential operation equipment
For gravity-type filters, reverse osmosis devices, ion exchangers and other devices that require sequential operation, the control operations include automatic, single-step, remote manual, or manual on-site methods.
The automatic mode is the control mode that the system automatically completes a series of operations according to the operator's instructions. After the automatic cleaning or regeneration process of the equipment is started, a series of operations will be automatically performed according to the requirements of the step sequence table, including the acid and alkali in the acid and alkaline measuring tanks. After the cleaning or regeneration is completed, it automatically goes into standby state. When programmed, the failed device can automatically stop running. In the single-step mode, the system completes a certain step in the step list according to the operator's instructions, including the switch of the valve and the start-stop of the motor. Remote manual refers to the start and stop of the motor and the opening and closing of the valve with a mouse on the screen.
1.2 Control of pumps, fans and valves
For all electric/pneumatic valves, fans, pumps and other equipment in the process system, program (remote) control and local control can be performed. For pneumatic valves, control can also be performed on the solenoid valve box, providing necessary protection in the control logic. And locking means.
The control of the water pump and the fan are automatically interlocked to start, remote manual, manual in several ways. When the pump or fan installed in the mother pipe is in the automatic interlocking start mode, if a motor stops due to a fault during operation, the motor in the interlock standby state is automatically started.
1.3 Power Control
The control, measurement and protection of the factory power supply 380V incoming line and the contact circuit breaker in the area of ​​the chemical water treatment station are hardwired into the boiler make-up water treatment control system, and the switching of the power supply system in the area is realized in the boiler make-up water treatment control system. , monitoring.
2, display function
All status information of the control system is displayed on a 21-inch display. The screen includes process flow diagram screens, operation screens, alarm display screens, and process parameter curves. It can display the process flow of each subsystem separately and collect the operating conditions of the system at any time, and realizes equipment accident alarms, process analysis, and systems. Fault detection, alarm management, report generation, operating condition recording, system parameter setting, and operation of equipment.
2.1 Process Flow Chart Screen
The process flow picture includes the general picture of the subsystem, the diagram of each subsystem, etc.
The flow chart shows the status of the valves and motors through different colors. The measurement values ​​and engineering units of the relevant meters, as well as the cumulative values ​​of the relevant flows, are also displayed on the screen.
2.2 Operation screen
The screen for system operation includes a device operation screen and an equipment overhaul window.
The system operation screen includes operation buttons such as a device selection button, a single-step operation button, an automatic operation button, and a delay button. When the cleaning or regenerating step is performed, the time for this step will be displayed on the screen.
2.3 Service Status Setting Screen
For large devices such as ion exchangers, they can be set on the screen for maintenance. Equipment that is in the maintenance state, the operator can't perform any operation on it at the moment, and can be operated only when the maintenance state is cancelled. The maintenance screen includes all device buttons that can be set to service status. Click the button of a device to set it to the maintenance status. Equipment that is under overhaul status changes its color when it is overhauled.
2.4 Step time modification screen
The step time modification screen has all the relevant steps and the setting values ​​of various types of sequential operation devices.
3, failure judgment and interlock function
The control system can judge whether it is ineffective according to the effluent quality of the relevant equipment such as ion exchangers (needs the on-line monitor table), differential pressure at the inlet and outlet, accumulated flow, or cumulative operating time. The failed device will alarm and can automatically stop running.
4. Manual intervention in sequential control
When the sequential control step is performed automatically, manual intervention such as stepping and stepping may be performed as needed, and the time and sequence of the originally set steps may be temporarily changed.
5, the time can be modified online.
V. Selection of instruments and local control equipment
There are two sources of chemical water meters and on-site control equipment at Qinbei Power Plant. Some of them are supplied with process equipment, and some are provided by program-controlled equipment manufacturers.
1, solenoid valve box
The electromagnetic valve box is equipped with an air source isolation valve, a gas source triple piece, and a cartridge type dual-control solenoid valve (including a bus plate). Valve position indicators (two-color light: red for on, green for off), valve operation knobs, local/remote switching knobs, etc. are mounted on the front panel.
Reciprocating pneumatic cylinder valves, such as pneumatic butterfly valves and ball valves on site, are controlled by dual-control, two-position, five-way solenoid valves. Pneumatic diaphragm valves could have been controlled by two-position three-way solenoid valves. In order to reduce the number of solenoid valves for the control system in the unified system, all solenoid valves were controlled by dual-control five-way solenoid valves.
2, chemical analysis instruments: All adopt flow-type instrument. Both the silicon meter and sodium meter, on-line COD meter, and turbidity meter use imported products. Conductivity meters, pH meters, and acid-base concentration meters use domestic products. Analytical instruments are equipped with instrument cabinets, front glass door type, you can view the data at any time but also to facilitate the protection of the instrument.
3, other instruments
The transmitter is Rosemount 3051; the level gauge uses a two-wire ultrasonic continuous level gauge or remote magnetic level gauge; the flow measurement device uses the imported power-bar flow measuring device (outdoor installed measuring device is equipped with a straight connection Three valve group); The remote temperature measuring element adopts a two-wire integrated temperature transmitter to improve the signal anti-interference ability and reduce the PLC module type.
Sixth, the design process should learn from the problem
In the chemical water program control design, the following issues are worth paying attention:
1. All the equipments and instruments in the Chengbei Power Plant Programmable Control are provided in complete sets. However, due to the large number of process systems, there are many control devices and instruments brought by the equipment manufacturers. Therefore, despite the uniform requirements in the selection, Inevitably there is a difference in the actual order, which causes troubles for the subsequent maintenance and spare parts purchase.
2. In the ultrafiltration area, the supplier of the ultrafiltration equipment comes with a set of PLCs. Some I/O points are advanced with their own PLC, and then transferred to the ultrafiltration remote I/O station. Before the program control bidding, there was no information on the ultrafiltration equipment with its own PLC, so it was impossible to foresee it. It was suggested that when the process system was tendered, it was required that any PLC with its own PLC should indicate the detailed I/O content of the PLC at the time of bidding and provide A unified network interface; In addition, the process and program control bidding time should be as far apart as possible to improve the accuracy of the data.
3. The rationality of I/O point allocation. The water area is divided into several subsystems, and the subsystems are divided into local and remote stations. Therefore, the distribution of I/O points should be considered more carefully. It is necessary to take into account the integrity of the system and to consider the distance. Save on cables. In this design, I feel that some I/O points are not very convenient. For example, the power circuit of the pump is in the MCC cabinet, some in the PC segment, and the PC in the laboratory floor. However, the program-controlled manufacturers do not understand the electrical system. The interface is to allocate I/O points according to the location of the pump room.
4. Anti-jamming of remote I/O network in field applications
In the IDAS remote I/O network, the communication module, the front-end unit, and the communication line are all electrically isolated. There is no common ground problem between the front-end units, and mutual interference between the front-end units is completely avoided. The problem of ground return flow makes the entire network in a “full-floating†state and ensures reliable network communications.
The communication between the communication module and the FEP uses a special modulation and demodulation circuit and a balanced differential transmission method. The transmission level is high, peak-to-peak up to ±12V (RS485 transmission level is ±5V), plus perfect The verification method and automatic retransmission technology greatly improve the anti-interference ability of network communications. The most important point is that this special communication method ensures that the front-end and front-end machines do not communicate with each other, further ensuring the reliability of data transmission.
5. Fault self-diagnosis and online setting of remote I/O system
Through the extended serial port on the communication module, the user can modify or set the parameters of the front-end computer online without interruption of the data transmission of the DCS system. At the same time, the user can also observe the self-diagnosis information of the network online, which brings about extreme operation and maintenance of the system. Great convenience.
IV. Concluding remarks
To sum up, the communication module can ensure the real-time data transmission in the connection of remote I/O and DCS systems, increase the transmission level to enhance the anti-interference ability of the communication, and reduce the DCS system to the remote I/O. Functional burden. After a period of electricity, the actual use of the situation, convenient transfer, reliable communication, small size, easy installation and positioning, for the remote I / O and DCS system, reliable, fast connection has played an integral role.
Suzhou Sikor Industry Co., Ltd. , https://www.sikor-group.com