The principle of generation: in the condition that the material has good plasticity and the amount of feed is large, the joint between the outer edge and the arc edge is basically a joint-shaped chip. However, during the additional deformation process in which the thicker chips are fanned out in the direction of the circular arc, the chips are pulled into knots and are integrated with the outer blade strips.
2 Factors and control of chip shape
1) The influence of the bit shape parameter on the shape of the chip, as shown in Figure 1.
a. Arc radius R:
R is too small: the formation of the chip point sharp angle is small, when the ξ < 150 °, the chips are easy to separate, the outer blade is out of the band-like debris, and the arc blade leaves the fan-like block.
R is too large: the formation of the chip point sharp angle is large, when the ξ> 170 °, the outer edge, the arc blade is easy to connect into one, and the short spiral fan-shaped chip.
R is moderate: when ξ=155~165° is formed, the angle between the outer blade flow direction and the adjacent arc blade flow direction is small, and the time is evenly divided. This is the condition for generating the “6†shaped chip. The optimum corner angle is related to factors such as material toughness and chip thickness, and is not constant. It can be inquired through trial and error.
b. Inner and outer edge height difference h
When the arc edge is deep, the outer edge and the arc edge form a natural chip point, and the outer blade has strip-like debris, and the arc blade has block-like debris. When the arc edge is shallow, the outer blade and the arc blade shape are not natural chipping points, and the chips are integrated to form a short spiral fan blade.
The depth of the arc edge is controlled by the vertical height difference h between the inner and outer blades. When the h value is proportional to the feed amount (cutting thickness), it is generally suitable to control the h value to be about 0.8f.
c. Outer blade front angle:
When the outer edge angle 2φ is too small (2F<125°), it is difficult to grind out ξ=150~165° sharp angle. The chips are easy to roll in the chip pocket and should not be excluded. Practical experience shows that 2φ=135°~140°, the chip outflow direction is close to the axis of the drill bit, which is beneficial to chip removal. Moreover, it is easy to form a large corner and control the occurrence of "6" chips.
The four parameters of the arc radius R°, the inner and outer edge vertical height difference h, the chip point sharp angle ξ, and the outer blade edge angle 2φ are related. Usually R is determined by the radius of the sharpening wheel radius. After selecting 2φ, h and ξ can be controlled by adjusting the process parameters of the bit sharpening machine.
2) Influence of material toughness on chip shape
The material has high toughness and the corners must be ground to make the chips separate. Otherwise the chips are not evenly divided. The material has low toughness and the corners should be ground larger.
3) Influence of tool wear on chip shape
After the edge of the drill blade is flattened or chipped, the actual flaw increases. When the actual x is too large (> 165 °), it can cause the change of the chip shape from the minute to the connection. Therefore, the standard or durability of the bluntness of stainless steel chip breakers should be based on the change in chip shape. The shape of the chips changes from a 6-shape to a short block, and the knife should be changed. We have had accidents due to the flattening of sharp corners and the short, short blocky debris that has broken the drill bit.
4) Influence of the alignment error of the chisel edge on the chip shape
The misalignment of the chisel edge reflects the enlargement of the diameter of the borehole, causing the secondary blade to work unilaterally, causing the negative edge of the drill bit to wear. This abnormal damage greatly reduces the life of the drill bit.
The cross-blade misalignment causes the two-edge cutting pattern to change, one side cutting double-thickness chips, and the other side cutting thinner chips. The double-thickness of the chips is only on the chip steel bars. The chips are thick and hard, and they are changed into long strips of chips, which are difficult to form 6-shaped chips.
5) Influence of cutting amount on chip shape
Increase the infeed, the chips become thicker, and it is easy to generate blocky chips. On the contrary, it is easy to form banding chips.
Changing the cutting speed of the drill has a slight influence on the cutting deformation. Generally, the cutting speed of high speed steel drill bits cannot be greatly changed. However, some stainless steels are very sensitive to chip shapes, and reducing the number of bit revolutions is beneficial for generating blocky chips.
3 Conclusion
Analysis of the results of the drilling test shows that the "6" shaped chips are the best among the various chip forms. Short spiral ribbons are also acceptable. Other types of chips such as long strips, swarfed chips, and flowered spiral strips should be prevented.
1) Control to generate "6" shaped chips, the conditions that should be met when using the drill bit reasonably are:
Control the bit shape parameters of the drill: front angle 2F=135~140°, outer blade length L=0.25d, sharp point of the chip point x=155°~165°, vertical height difference between outer edge and arc edge h=0.8f
2) Control the symmetry accuracy of the drill sharpening: the chisel edge is moderate, and the outer blade, inner blade and arc edge are as small as possible. Generally, a drill sharpener is used to measure the internal and external edge runouts online. It is feasible that the chisel edge misalignment error is <0.02 to 0.03 mm. Manually sharpening the left and right edges is difficult to symmetry, which inevitably produces chips with reinforcing bars to accelerate the wear of the drill bit.
3) Choose a reasonable amount of drilling: Drilling stainless steel should use a lower cutting speed, moderate feed. Ordinary high speed steel drills are recommended to be v = 15 ~ 18m / min f ≈ 0.015d mm / r, using sufficient emulsion to cool. This allows the tool to last for about 100 minutes.
2 Factors and control of chip shape
1) The influence of the bit shape parameter on the shape of the chip, as shown in Figure 1.
a. Arc radius R:
R is too small: the formation of the chip point sharp angle is small, when the ξ < 150 °, the chips are easy to separate, the outer blade is out of the band-like debris, and the arc blade leaves the fan-like block.
R is too large: the formation of the chip point sharp angle is large, when the ξ> 170 °, the outer edge, the arc blade is easy to connect into one, and the short spiral fan-shaped chip.
R is moderate: when ξ=155~165° is formed, the angle between the outer blade flow direction and the adjacent arc blade flow direction is small, and the time is evenly divided. This is the condition for generating the “6†shaped chip. The optimum corner angle is related to factors such as material toughness and chip thickness, and is not constant. It can be inquired through trial and error.
b. Inner and outer edge height difference h
When the arc edge is deep, the outer edge and the arc edge form a natural chip point, and the outer blade has strip-like debris, and the arc blade has block-like debris. When the arc edge is shallow, the outer blade and the arc blade shape are not natural chipping points, and the chips are integrated to form a short spiral fan blade.
The depth of the arc edge is controlled by the vertical height difference h between the inner and outer blades. When the h value is proportional to the feed amount (cutting thickness), it is generally suitable to control the h value to be about 0.8f.
c. Outer blade front angle:
When the outer edge angle 2φ is too small (2F<125°), it is difficult to grind out ξ=150~165° sharp angle. The chips are easy to roll in the chip pocket and should not be excluded. Practical experience shows that 2φ=135°~140°, the chip outflow direction is close to the axis of the drill bit, which is beneficial to chip removal. Moreover, it is easy to form a large corner and control the occurrence of "6" chips.
The four parameters of the arc radius R°, the inner and outer edge vertical height difference h, the chip point sharp angle ξ, and the outer blade edge angle 2φ are related. Usually R is determined by the radius of the sharpening wheel radius. After selecting 2φ, h and ξ can be controlled by adjusting the process parameters of the bit sharpening machine.
2) Influence of material toughness on chip shape
The material has high toughness and the corners must be ground to make the chips separate. Otherwise the chips are not evenly divided. The material has low toughness and the corners should be ground larger.
3) Influence of tool wear on chip shape
After the edge of the drill blade is flattened or chipped, the actual flaw increases. When the actual x is too large (> 165 °), it can cause the change of the chip shape from the minute to the connection. Therefore, the standard or durability of the bluntness of stainless steel chip breakers should be based on the change in chip shape. The shape of the chips changes from a 6-shape to a short block, and the knife should be changed. We have had accidents due to the flattening of sharp corners and the short, short blocky debris that has broken the drill bit.
4) Influence of the alignment error of the chisel edge on the chip shape
The misalignment of the chisel edge reflects the enlargement of the diameter of the borehole, causing the secondary blade to work unilaterally, causing the negative edge of the drill bit to wear. This abnormal damage greatly reduces the life of the drill bit.
The cross-blade misalignment causes the two-edge cutting pattern to change, one side cutting double-thickness chips, and the other side cutting thinner chips. The double-thickness of the chips is only on the chip steel bars. The chips are thick and hard, and they are changed into long strips of chips, which are difficult to form 6-shaped chips.
5) Influence of cutting amount on chip shape
Increase the infeed, the chips become thicker, and it is easy to generate blocky chips. On the contrary, it is easy to form banding chips.
Changing the cutting speed of the drill has a slight influence on the cutting deformation. Generally, the cutting speed of high speed steel drill bits cannot be greatly changed. However, some stainless steels are very sensitive to chip shapes, and reducing the number of bit revolutions is beneficial for generating blocky chips.
3 Conclusion
Analysis of the results of the drilling test shows that the "6" shaped chips are the best among the various chip forms. Short spiral ribbons are also acceptable. Other types of chips such as long strips, swarfed chips, and flowered spiral strips should be prevented.
1) Control to generate "6" shaped chips, the conditions that should be met when using the drill bit reasonably are:
Control the bit shape parameters of the drill: front angle 2F=135~140°, outer blade length L=0.25d, sharp point of the chip point x=155°~165°, vertical height difference between outer edge and arc edge h=0.8f
2) Control the symmetry accuracy of the drill sharpening: the chisel edge is moderate, and the outer blade, inner blade and arc edge are as small as possible. Generally, a drill sharpener is used to measure the internal and external edge runouts online. It is feasible that the chisel edge misalignment error is <0.02 to 0.03 mm. Manually sharpening the left and right edges is difficult to symmetry, which inevitably produces chips with reinforcing bars to accelerate the wear of the drill bit.
3) Choose a reasonable amount of drilling: Drilling stainless steel should use a lower cutting speed, moderate feed. Ordinary high speed steel drills are recommended to be v = 15 ~ 18m / min f ≈ 0.015d mm / r, using sufficient emulsion to cool. This allows the tool to last for about 100 minutes.
EDM graphite, also known as graphite block for EDM, is a new type of material, which is now more and more widely used in the precision mold processing industry. At present, in mold processing plants in developed European countries, more than 90% of mold processing electrode materials are graphite. Copper, the once dominant electrode material, has almost lost its advantages compared with graphite electrodes.
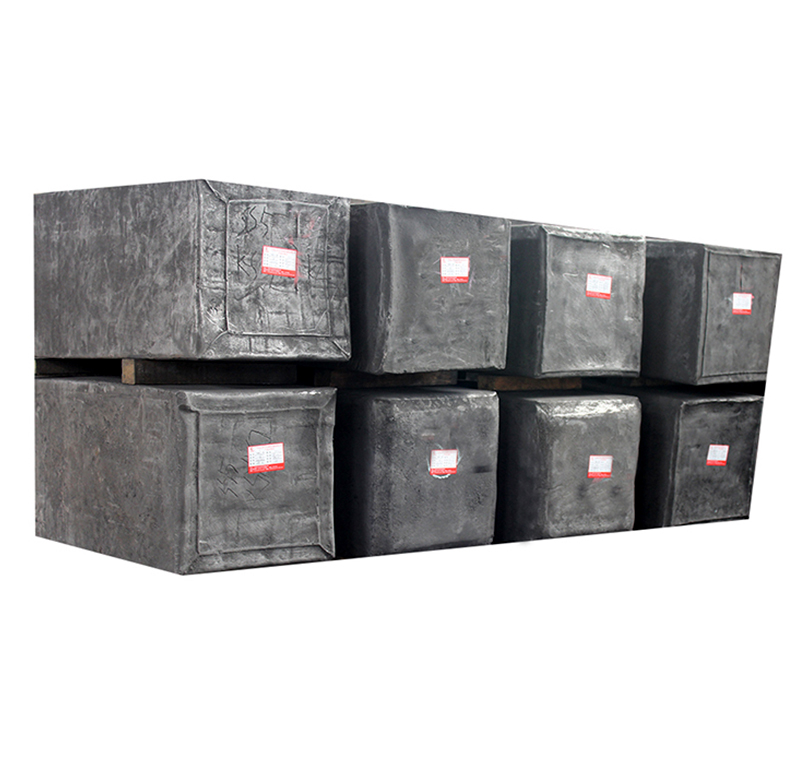
Our isostatic graphite and Molded Graphite were tested at the National Electrical Carbon Products Quality Supervision and Inspection Center. The main physical and chemical performance index as follows: the compressive strength--125 mpa, shore hardness -- 65 degrees, resistivity --12 mu Ω m. At the same time, the 10μm,8μm,6μm,4μm products have already began Large-scale production,.and unanimously acknowledged by customers. The 2μm,1μm graphite products are under trial. Our company high quality of isostatic pressing special graphite yield above 90%, far ahead of industry the yield of 70%, the first in the country.
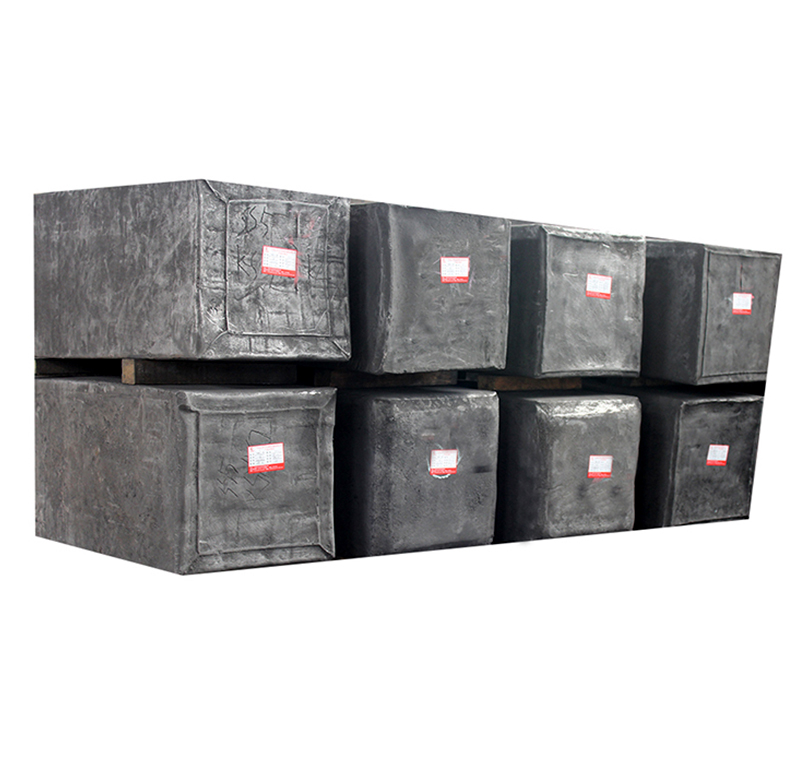
Our isostatic graphite and Molded Graphite were tested at the National Electrical Carbon Products Quality Supervision and Inspection Center. The main physical and chemical performance index as follows: the compressive strength--125 mpa, shore hardness -- 65 degrees, resistivity --12 mu Ω m. At the same time, the 10μm,8μm,6μm,4μm products have already began Large-scale production,.and unanimously acknowledged by customers. The 2μm,1μm graphite products are under trial. Our company high quality of isostatic pressing special graphite yield above 90%, far ahead of industry the yield of 70%, the first in the country.
Company main products:
2.Molded graphite block
3.Graphite rod
4.Graphite tube
5.Graphite plate
7.Graphite crucible
Customized High Pure and density graphite products/graphite block for EDM
Edm Graphite,Graphite Block For Edm,Edm Graphite Electrodes,Isostatic Graphite Column
Henan Carbons New Material Technology Co., Ltd. , https://www.kygraphiteblock.com